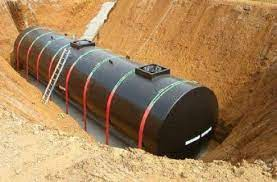
Backfilling of fertilizer tank
The fertilizer trough is that part of the space that is excavated to provide a working surface, such as the space between the outer wall of the basement of a building or the outer wall of the foundation and the edge of the foundation pit. The backfilling of the fertilizer tank requires the strength of the backfill material to be higher than 1MPa. For this purpose, foam concrete with a wet bulk density of 500kg/m3 and a dry bulk density of 400kg/m3 is designed. Using a nano foaming agent, the minimum cement consumption can be reduced to 260 kg/m3, saving raw materials. The cost is about 40%, the thermal insulation capacity is improved by 20-30%, and the actual cement consumption is saved by 190kg/m3. While significantly saving costs, it has made a practical contribution to reducing carbon emissions (0.93 tons of carbon dioxide is emitted per ton of cement production).
Using nano-foam concrete to backfill the fertilizer tank can not only save a lot of material costs but also save labour costs and speed up the construction progress. Due to the lightweight of foam concrete and the high fluidity of the slurry, pumping construction is used. Several fixed pumping pouring points are set up around the fertilizer tank for continuous pouring. Only 4-5 general workers are needed on-site, and the labour intensity is not high. It is necessary to regularly add foam, operate mixing and pumping equipment, and conduct construction inspections. One set of equipment can pour 500 cubic meters of foam concrete every day, greatly improving construction efficiency. 2. Roadbed (widening) filling With the rapid development of my country’s economy, a large number of traffic infrastructure projects are built every year; on the other hand, for road sections with relatively busy road conditions, large traffic volumes, and long operating hours, the road surface width cannot meet the increasing demand. With the increasing traffic volume, it is particularly necessary to reconstruct and expand this type of highway. In reconstruction and expansion construction, highway widening is more common, which is the main means to improve highway transportation capacity.
In roadbed filling construction, earth and stone backfilling is often used. However, this backfilling method will increase the vertical pressure, so the bottom bearing capacity is very high. However, there are large areas of deep, soft soil in our country with low foundation-bearing capacity, large settlement deformation, and engineering diseases. It is often difficult to build or widen roadbeds in this area. Problems such as uneven settlement will be encountered, which will affect the quality of the road and bring certain hidden dangers to the safe operation of the highway. Therefore, reducing uneven settlement is the key to the success of new reconstruction projects. Nano-foam concrete provides a new way to solve this problem. It is lightweight, stable, has good thermal insulation, and is less affected by environmental factors. It can reduce load pressure and uneven settlement during the roadbed filling process. In turn, it improves the construction quality, reduces the difficulty of the operation, improves the safety of the workers, shortens the construction period, and saves land resources. In the reconstruction and expansion of highway projects it plays a certain role in roadbed filling, foundation treatment, etc. Engineering applications Broad prospects.
There have been many actual engineering cases of foam concrete used in roadbed filling, and experts and scholars have also published many papers and articles verifying the feasibility and advantages of foamed concrete in roadbed filling. Subgrade filling generally requires the strength of foam concrete to be about 1MPa. When the depth below the road surface is more profound, the required strength is lower, and a minimum of 0.4MPa can meet the requirements. Using our company’s nano-foaming technology, nano-foam concrete’s dry density of 300~400kg/m3 can meet the strength requirements, and the amount of cement can be greatly reduced. Therefore, compared with other backfill materials and ordinary foam concrete, a lot of material costs are saved.
Mine backfilling
China is a large country rich in mineral resources. After the year of 1949, the mining industry has developed rapidly. However, large-scale development has also brought about ecological and environmental problems. Remote sensing survey and monitoring data show that as of the end of 2018, more than 54 million acres of land were occupied and damaged by mining in the country, of which more than 20 million acres were occupied and damaged by ongoing mines, and more than 34 million acres were occupied and damaged by historical mines. With the increasing advancement of ecological civilization construction, mine restoration has become an essential environmental governance issue. Abandoned mine pits can be restored into natural ecological tourism landscapes, or they can be backfilled and covered with soil to maximize the value of cultivated land, or they can be backfilled to provide more construction land for economic development.
Mine backfilling generally uses earthworks, industrial waste or construction waste as backfill materials. It requires a large number of construction vehicles and equipment such as muck trucks, bulldozers and excavators. The transportation cost is high, the backfilling period is long, and the quality of the backfill is difficult to control, which may occur later. The risk of settlement, in addition, earth and stone resources are effective, and it is usually necessary to bid separately to determine the source of soil entering the site or to excavate and fill it nearby, which is also equivalent to destroying the soil layer in other places. Our company’s nano-foam concrete provides a new solution for mine backfilling, which has the advantages of low cost, simple and fast construction, and guaranteed strength. Nano-foam concrete is used to backfill mines. The amount of cement is small. Waste industrial waste slag powder can also be fully used to replace part of the cement to further reduce costs. It can be pumped directly for backfill construction without going down to the mine for work, and the safety risk is small.
Roof insulation
Our country is currently in an important period of building energy conservation, and the energy consumption of thermal bridges in building exterior walls and roofs accounts for a large proportion of construction energy. At present, most of the organic materials with good thermal insulation performance on the market are organic materials. However, organic insulation boards have many seams. When the waterproof layer leaks, water will flow along the seams. It is difficult to find the leakage point and repair it. The material itself has problems such as flammability, easy aging, high strength, and high water absorption, which makes the energy-saving measures taken on the roof not achieve the expected results. Our inorganic nano-foamed concrete has excellent thermal insulation properties, good sound insulation properties, lightweight, high strength, fire protection level A and high durability. It is also currently widely used in roof insulation and other insulation materials. It also has many technical advantages.
For example, our nano-foam concrete has good pumpability during the construction process and can be poured on-site to the construction site. It is closely integrated with the main structural layer, simplifying the construction process and shortening the construction period. It can be used as a thermal insulation layer on the roof without leaving any separation joints. And breathable tubes.
Foundation cushion pouring
The traditional foundation cushion is poured with C15 or C20 ordinary concrete. This construction technology is suitable for geology with the high bearing capacity of the original soil layer. If it is applied to the silty soil layer, a large amount of replacement and filling will be required, and mechanical construction will be laid in advance. The way. At present, the domestic concrete cushion pouring technology on silty soil is not yet mature. Using traditional techniques wastes construction time and increases costs. In order to improve project progress and economic benefits, it is necessary to choose a more cost-effective construction technique.
By adjusting the mix ratio, we designed nano-foam concrete with a compressive strength of 1~5MPa. The strength is significantly greater than the concrete base pressure (0.025MPa), effectively ensuring the integrity of the foam concrete cushion. Due to the lightness of the foam concrete, it can be floated. The silt soil surface and the construction surface are naturally level. After solidification, various ground materials can be directly pasted. The porosity of foam concrete gives it a lower elastic modulus, which has good absorption and dispersion of impact loads and improves the overall performance. Earthquake resistant. Taking advantage of the advantages of nano-foam concrete such as low density, fast molding, convenient operation, and effective combination with silt, it can solve the problem that ordinary concrete cushion cannot be poured on flow-plastic silt soil layer while ensuring the strength of the cushion, and obviously fasten the construction time, speed up the project progress, and improve economic benefits.
Bathroom/basement backfilling
Ceramics can be used as bathroom backfill material. It has the advantage of absorbing odour and water and is also relatively light in weight. However, ceramsite itself does not have the ability to deal with odors. Over time, the smell in the bathroom will become stronger and stronger. Moreover, ceramsite construction is complex and difficult to maintain. The material is loose and can easily lead to leakage. The price of ceramsite is also relatively high.
Foam concrete is used as a backfill in the bathroom. Its advantages are that it is relatively light in weight, does not crack or settle, has high fluidity, can be levelled independently, and is simple to construct. It can solve the problem of water accumulation in the bathroom caisson and reduce the overall load of the building. It is more suitable for bathroom decoration. Backfill material.
Roofing slope
Foam concrete is used for roofing inclines and has the benefits of lightweight, fast construction speed, and small cost. The slope is generally 10mm/m. The thickness is 0.03-0.2 m, and foam concrete with a thickness of 800-1200kg/ m3 is utilized.
On-site pouring of walls
Foam concrete is foamed and poured on-site to be used as non-load-bearing walls of buildings, changing the current method of building walls with prefabricated blocks. The wall has good integrity, simple construction, low labour intensity, and low cost. It also has the advantages of lightweight, thermal insulation, waterproofing and anti-seepage. It is an alternative to the current traditional wall.
Retaining wall
Mainly used as a rock wall for the harbour. Foam concrete is used as a lightweight backfill material behind the quay wall to reduce the vertical intercept load and also reduce the lateral load on the quay wall. This is because foam concrete is a rigid body with great bonding properties. It does not exert lateral pressure on the quay wall along the perimeter. The settlement is reduced, and the maintenance costs are reduced accordingly, thus saving a lot of expenses.
Foam concrete can also be used to improve the stability of embankment slopes by replacing part of the soil on the slope. By reducing the mass, the forces affecting the slope stability are reduced.
Pipeline backfill
Abandoned oil tanks, pipelines (containing crude oil and chemicals), sewage pipes and other cavities underground can easily lead to fires or landslides. Using foam concrete backfill can solve these problems at a low cost. The density of foam concrete relies on the diameter of the pipe and the water level, generally 600-1100kg/m3.
Supplier
TRUNNANO is a supplier of foaming agents and relative concrete materials with over 12 years experience in nano-building energy conservation and nanotechnology development. It accepts payment via Credit Card, T/T, West Union and Paypal. Trunnano will ship the goods to customers overseas through FedEx, DHL, by air, or by sea. If you are looking for high-quality concrete additives, please feel free to contact us and send an inquiry.